The aerospace industry is already a concentrated expression of a country's comprehensive national strength. In the process of developing and manufacturing national defense equipment, Beijing Xinghang Electromechanical Equipment Co., Ltd. has adopted a number of advanced tool products, successfully solved the processing difficulties brought by difficult-to-machine materials, and improved the overall processing efficiency by 20%. The many benefits of high-quality tools are still in use today.
Founded in 1960, Beijing Xinghang Electromechanical Equipment Co., Ltd. (hereinafter referred to as “Xinghang Electromechanicalâ€) is located in the western suburbs of Beijing. It is a national large-scale high-tech enterprise affiliated to the Third Research Institute of China Aerospace Science and Industry Corporation. The company covers an area of ​​290,000 square meters and has a total asset value of more than 2.2 billion yuan. The existing staff is about 1,500. Based on advanced aerospace technology and equipment, the company develops a wide range of precision cutting and forming parts, precision casting molded parts and welded parts. Xinghang Electromechanical Co., Ltd. takes the development and production tasks of national defense defense products as its main business. It has undertaken the research and production tasks of several national key defense products and filled many gaps in the field of national defense equipment.
Beijing Xinghang Electromechanical Equipment Co., Ltd., a subsidiary of China Aerospace Science and Industry Corporation, is a state-owned large-scale industrial enterprise.
The company has won more than 50 provincial and ministerial level scientific and technological progress awards. These awards reflect the research and development level of Xinghang Electromechanical, and also affirm the ability of Xinghang Electromechanical in research and development and manufacturing. According to Dr. Jiang Tao, the project director of the Star Aviation Electromechanical Technology Center, Xinghang Electromechanical has very high standards for its own technical requirements. First, it is due to the particularity of its product field, the high standard requirements of the flight products themselves. The willingness to continuously transform and upgrade the product. At present, the company has multi-model, multi-series hot and cold processing equipment and precision testing, measurement, physical and chemical testing equipment, has now formed a complete supporting casting, sheet metal, riveting, welding, hot table processing, physical and chemical testing, CNC machining, final assembly , testing and CAD/CAM integrated manufacturing systems and other modern technology and equipment capabilities.
The key to the tool is the service life.
The aerospace industry is known as the apex of the manufacturing pyramid, and the production of aerospace products represents cutting-edge manufacturing, regardless of processing or processing materials. As one of the branches, the national defense equipment manufacturing industry is also regarded as a high-tech industry, and it is also a concentrated expression and an important symbol of a country's comprehensive national strength. With the development of science and technology, the requirements for lightweight materials and special properties (such as stealth) of national defense equipment are also constantly increasing. Therefore, the proportion of difficult-to-machine materials such as titanium alloys and composite materials is increasing. This also caused a lot of processing problems.
Titanium alloys are widely used because of their high strength, good corrosion resistance and high heat resistance. In titanium alloy processing, the choice of tools is critical and will have a decisive influence on the processing quality of titanium alloys. The ideal tool for processing titanium alloys must have high thermal hardness, good toughness, good wear resistance, high thermal conductivity and low chemical activity, especially in milling, the tool should also have good resistance. Impact.
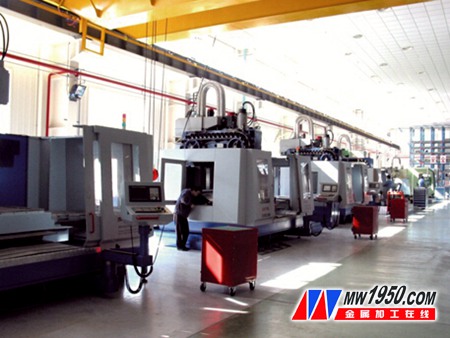
In all the processing tasks of Xinghang Electromechanical, the use of titanium alloys accounts for a relatively high proportion.
Mostly frame and rotary parts for flying products
Among all the processing tasks of Xinghang Electromechanical, the use of titanium alloys occupies a relatively high proportion, mostly for the frame type of flying products and the rotary parts. "Our cooperation with Walter dates back to 2005. Since the model was introduced, Walter's tool products have been used for nearly ten years." Mr. Yang Hongyu, a technician specializing in tool processing at Xinghang Electromechanical, recalled . The specifications of the titanium alloy frame products of Xinghang Electromechanical are not large. The blanks are similar to the shape of the wing, flat, and the front and back sides need to be profiled, and in order to reduce the quality of the products, there are many grooves and parts for weight reduction design. The middle part is also basically a hollow design for weight reduction. The process flow of the part is not complicated. Mr. Yang Hongyu said that the blank is first handed to the fitter to scribe, because the special shape of the part can not be loaded, so the next step is to machine the part of the chuck, then the rough milling part Positive and negative, stabilized, then fine line, chuck finishing and finishing on both sides.
Starting from the heat treatment, all the process steps are counted. The processing time of a titanium alloy part is about 60 hours, and the time of the metal working part is about 40 hours. Three Walter ball-end inserts are used for processing such a workpiece. “From our experience, Walter has the longest tool life. We have compared it with several imported blades. The life of the tool is the same at Walter's ball and knives at the same speed and feed. The longest, the best performance.†Mr. Yang Hongyu clearly pointed out that although the poor thermal conductivity of titanium alloy will lead to faster tool wear, Walter's one knife can achieve a service life of 4 hours during roughing. 8 hours, and other manufacturers can not meet this standard.
In the 10 years of using Walter tool products, Star Air has compared it with several imported blades.
Walter's ball-end knives have the longest service life and best performance at the same speed and feed rate.
At present, the Walter tool used by Xinghang Electromechanical is the P3204-D16 WSM36 ball-end blade with F2139 ball-end cutter. Walter profiling precision milling cutter F2139 is a high-precision tool for cavity finishing. Extremely precise four-sided grinding inserts are available in a variety of cutting materials and groove types to ensure optimum surface quality of the workpiece; The groove type and coating technology of the machined material prolongs the service life of the tool; in addition, the symmetrical body structure meets the requirements of high-speed machining. Walter is now also equipped with a solid carbide shank for this milling cutter, which provides shock absorption during long overhangs. Based on the above conditions, the tool can be perfectly matched to the specified machining conditions. Moreover, the WSM36 blade used by Xinghang Electromechanical is a new material modified by Walter technology. The base material of this material is ultra-fine cemented carbide grain, and the bottom layer of the blade coating is TiAlN material, which improves the resistance to flank wear. In the middle is PVD γ-Al2O3 coating, which improves the plastic deformation and micro chipping resistance. The surface decorative coating is ZrN, and the thickness of the whole coating is only 4-5μm to ensure the sharpness of the cutting edge. So far, the product has been in service for a decade in the processing of Xinghang electromechanical titanium alloy parts, and its outstanding tool life is the key to conquering Xinghang Electromechanical.
Tool is the cornerstone of processing efficiency
In all parts of Xinghang Electromechanical, in addition to the relatively large proportion of titanium alloy, the proportion of aluminum alloy has reached 40%. These aluminum alloy parts are mostly thin-walled, deep-cavity parts. Compared with titanium alloys, aluminum alloys have good thermal conductivity and low hardness, so the processing is relatively easy, and the requirements for tools are relatively low. In the processing of aluminum alloy parts, Xinghang Electromechanical requires high strength and high toughness of the tool. There are more cemented carbide tools used here. In addition to this, there is a clear requirement for processing efficiency. Dr. Jiang Tao said: "Because the R&D cycle of equipment is getting shorter and shorter, this requires a corresponding improvement in the manufacturing level, especially for the processing efficiency." Through the use of Walter tools, Xinghang Electromechanical Aluminum The processing efficiency of the alloy parts has been improved by 20% as a whole, and the improvement of the efficiency has also reduced the overall processing cost, which has brought great benefits to the manufacture of the products of Xinghang Electromechanical.
Jiang Tao, Head of Pre-Research Project, Technology Center
The shape of the aluminum alloy parts processed by Walter's tool products is similar to a rectangle, but there are many different sizes of cavities. The depth of the cavity is generally between 100 and 120 mm. Therefore, the hardness and wear resistance of the tool during machining are high. Sex, impact resistance, and vibration are all factors to consider. These cavities are mostly standard rectangles. Before the cooperation with Walter, the machining shop often encounters the broken knife when machining the corners of the cavity. Because the depth of the cavity is large, the vibration of the tool is easy to cause the broken knife, and the corner The part is the rounded corner of R8, and the corner angle is about 90°. After using Walter's milling cutter, this situation has been greatly improved, not only the vibration is eliminated, but also the surface processing quality is greatly improved. Therefore, Walter is the earliest cooperative tool manufacturer of Xinghang Electromechanical, and this cooperation lasted for ten years.
Huge space for cooperation
Ding Guozhi, Technical Manager of CNC Machining Workshop
At present, there are many types of difficult-to-machine materials in the processing workshop of Xinghang Electromechanical, such as high-temperature alloy, tungsten-nickel iron and so on. Mr. Ding Guozhi, technical director of Xinghang Electromechanical CNC Machining Workshop, said that the proportion of superalloys has now reached 15%, and the improvement of processing efficiency needs to be solved urgently. “Because of the product needs, some small cabin parts we are processing now It is made of high-temperature alloy. The thermal conductivity of superalloy is very poor. It is only one-seventh of the thermal conductivity of titanium alloy. It can be seen that it is difficult to machine." This kind of machining will cause rapid and rapid wear of the tool, so the tool can Machining is the first step, and then the service life of the tool is considered, and then the machining efficiency of the tool is considered. “Now we use a knife to process superalloys. The basic tool life is over 20 minutes. If we can find tools that last for more than 1 hour, it will greatly improve our processing status, and the overall processing cost will be reduced. "Mr. Yang Hongyu thinks this is the biggest problem that is currently plaguing him.
Mr. Yang Hongyu, CNC Tool Manager, who is reading the Walter product brochure
The tool played a vital role in the processing of Xinghang Electromechanical. It turned out that some parts only need to be processed for about half a month in one process. Under the intervention of high-quality tools, this situation is basically eliminated. Of course, this improvement can be achieved not only by high-quality tooling products, but also by the tool suppliers' pre-services, such as tool selection recommendations and process improvements. Among all the relevant factors, Mr. Yang Hongyu believes that the most important thing is the communication of tool information and the trial of the product. “This link is very important. We need to use the latest tool grades, but we must first know what optimizations the tool suppliers have made. The other is the trial of the tool, there are new tools to launch, we hope to get the trial in the first time."
In fact, for these problems, Walter has given a good solution, such as the new brand Walter Multiply. This is an overall service concept and tool management is an important part. An important component of the tool management system is Walter's Tool Management Software (TMS), which provides a clear view of current stock levels, individual tool change cycles and accurate tool consumption. It also records the specific movement of each tool, from tool reception to installation, including assembly tools. Another benefit is the ability to inventory in TMS at the touch of a button by configuring cost centers, staff, shifts, and projects. In this way, the user can retrospectively estimate the actual tool cost incurred by the project of interest without any effort. The individualized service components of the tool management system, including the tool supply system, supply management, “cost per part†solution and inventory optimization, can be customized to the individual needs of the customer. In the near future, users only need to input the basic structural features and materials of the parts to be machined, and the software can automatically equip the user with the knife, which is in line with the idea of ​​Xinghang Electromechanical.
Sheet Metal Fabrication,Cnc Bending Parts,Metal Flat Bracket,Customized Sheet Metal Fabrication
JIANGSU TONGDE INTERNATIONAL TRADE CO.LTD. , https://www.tongdetrades.com